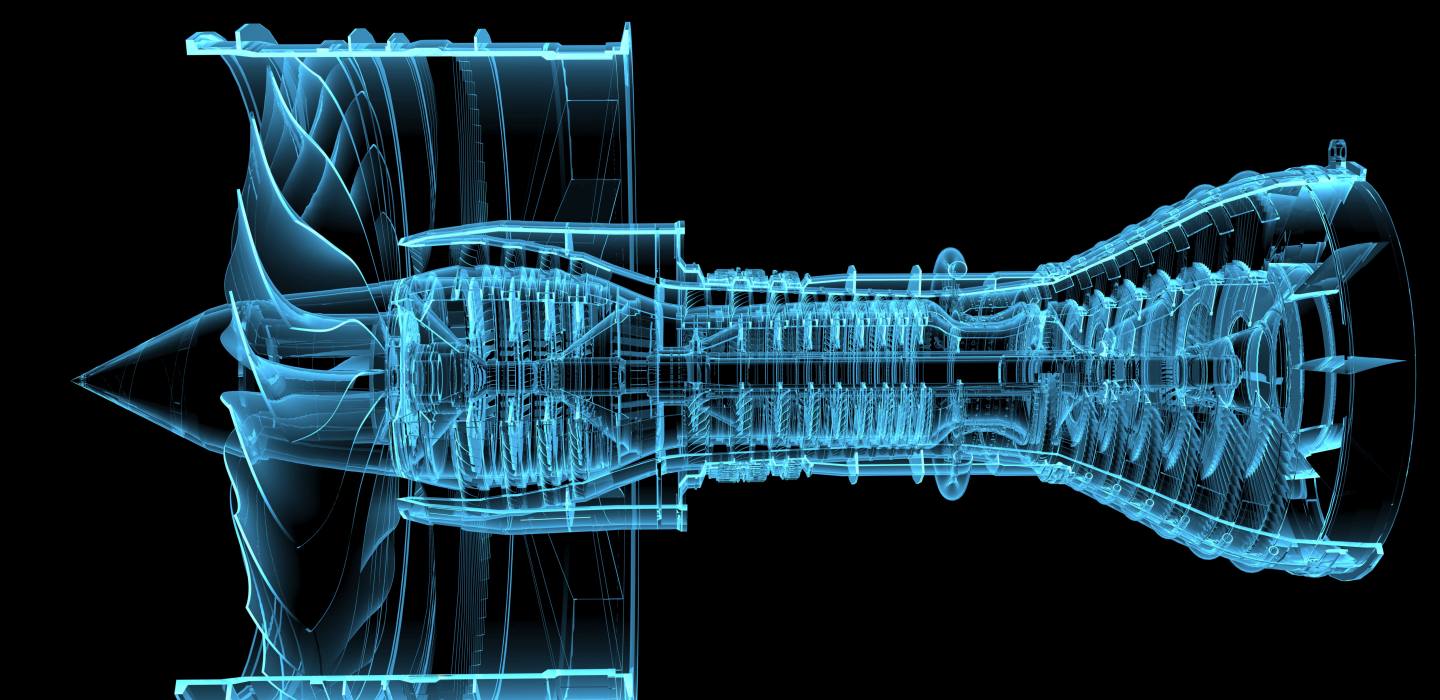
Technologies
ASP possesses cutting-edge aviation industry technologies and the expertise required for continuous development and investment, allowing for portfolio expansion and the ability to serve a broader customer base.
Currently, the company specializes in the following key processes:
- DRY ABRASIVE BLASTING
- SURFACE STRESSING BY –SHOT-PEEN
- BLENDING AND REMOVAL OF HIGH METAL PROCEDURES
- ELECTROCHEMICAL ETCH MARKING
- SWAB ETCHING
- ANTI-CORROSION SURFACE TREATMENT
- SPOT TOUCH-UP OF OXIDE FILM COATING ON ALUMINUM ALLOYS FOR PROTECTION – CHROMATE
- APPLICATION OF ANTI-EROSION AND POLYURETHANE PAINT
- MACHINING (CNC CONTROLLED DRILLING, MILLING, GRINDING)
- HIGH-TEMPERATURE FURNACE BRAZE AND HEAT TREATMENT
- SOLVENT DEGREASING, AQUEOUS, STEAM CLEANING, LIGHT-DUTY AQUEOUS, AND HEAVY-DUTY ALKALINE CLEANING
- TIG / RESISTANCE / SPOT WELDING AND BRAZING
- OXYACETYLENE TORCH BRAZING
- RIVETED JOINTS
- FLUORESCENT PENETRANT INSPECTION
- HARDNESS TESTING
These capabilities ensure high-quality solutions that meet the strictest industry standards.
Our capabilities
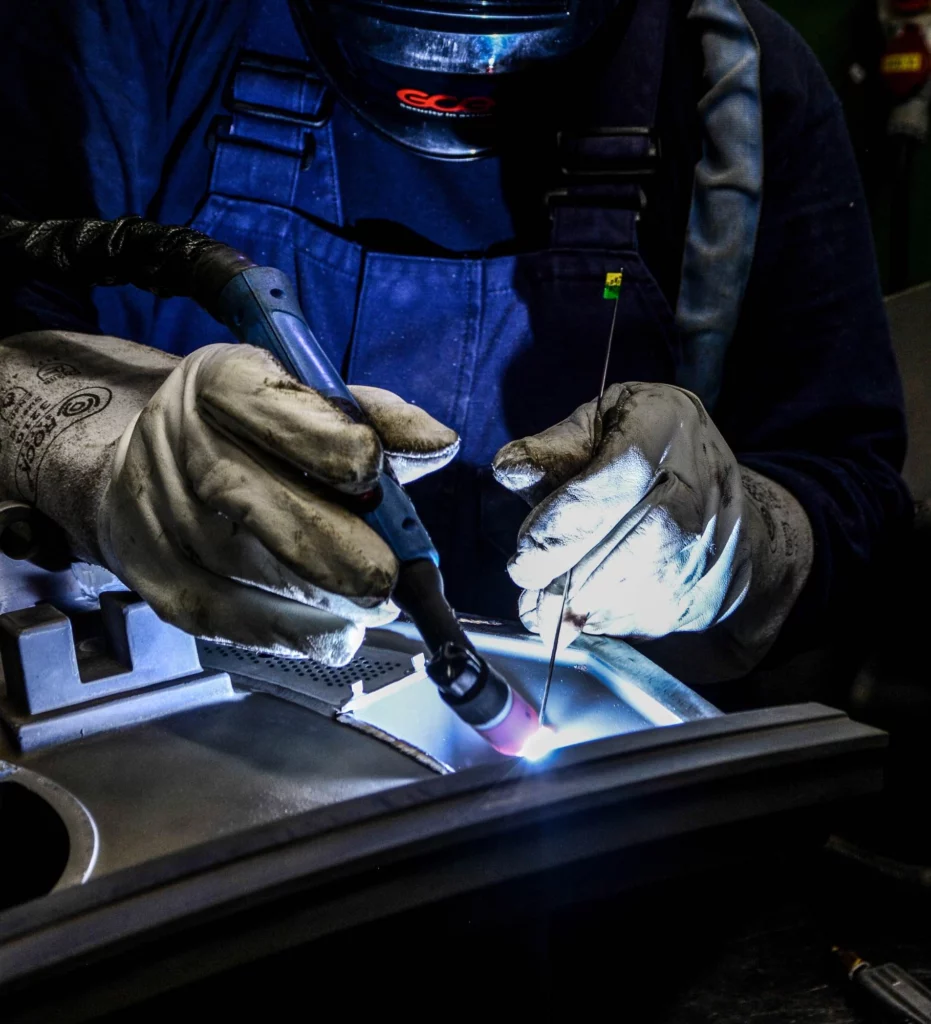
Welding
Welding and brazing are used to create an indissoluble bond between various metals. In terms of welds, the methods we use are Gas Tungsten Arc Welding (GTAW), also known as Tungsten Inert Gas (TIG) welding with different filler materials, resistance spot welding, and tack welding.
The brazing methods we use are vacuum furnace brazing and torch brazing.
Aero Space Power manufactures products of excellent quality that meet international and national standards in accordance with the traditions of the company. We pay attention to the special training of our employees and the continuous development of our equipment. Our business unit offers welding of superalloy materials as well as aviation services that require the highest quality of service. Tungsram welding owns leading technologies and skills.
Aero Space Power welders have experience in welding of structural carbon steel, stainless steel, aluminium, and other superalloys. Welding work is carried out at designated workstations (welding booths), but we also have portable welding infrastructure to perform on-site welding. Several welding procedure qualifications are available for the different material groups and welding procedures corresponding to different coatings.
Specifications
- QPRs & WPQs per AWS D17.1:
- Gas Tungsten Arc
- Welding
- Matr. Group: II. A (Austenitic Stainless Steel), III. B (Precipitation Hardenable Nickel-based alloys), VI. (Titanium alloys), VII. (Cobalt base alloys)
- PQRs & WPQs per ISO15614 & ISO9606:
GMAW (per ISO4063) - Matr. Group: 22 (aluminium, per ISO 15608)
- Matr. Group 1.1, 1.2 (per ISO 15608)
- PQRs & WPQs per certain OEMs requirements
GMAW & GTAW - Austenitic stainless steel, Nickel Base Alloy, Cobalt Base Alloy
- ASP also has ISO3834-2 certification
Heat Treatment
There can be numerous reasons to do heat treatment on metallic components. The fusion welding tends to cause undesirable mechanical property changes by having the microstructure changed driven by the localized heat exposure. A broadly utilized method for stress relieve and mechanical property restoration is heat treatment. There are also other unique application possibilities beyond that like the precipitation hardening as the result of a controlled solution & age heat treatment cycle. Aero Space Power’s vacuum furnace is capable of these heat treatment operations and has the capability for vacuum brazing too.
The ultimate vacuum level we can achieve is <0.5 Torr, and the available instrumentation enables us to monitor the temperature dispersion inside of the vacuum chambers by 3pc of control & 12pc of load thermocouples. Our furnaces meet the pyrometric requirements of AMS2750.
Read more
There are certain components available in both jet engines and gas turbines that has unique operating conditions and are exposed to special operating conditions. That can cause high stresses, thermal fatigue, and high-temperature oxidation, and that often ends in crack nucleation and crack propagation. The cracks are usually impacted by oxidation too.
Welding is an option to repair cracks, however only in moderation. A significant portion of hot gas path components can be repaired only by activated diffusion healing (ADH). This procedure may be accomplished successfully only if the cracks are free of oxides. Our heat treatment equipment has the capability to introduce H2 gas in partial pressure in a well-controlled manner to reduce the embedded oxides inside of the cracks. And once the cracks are clean the ADH is also something that is a perfect fit to our technologies as it is pretty much alike of brazing. This repair method provides cost effective solution to get high-value HPT parts back to serviceable condition and that can also extend the lifetime of turbine components to make long term service agreements more profitable.
Our capabilities
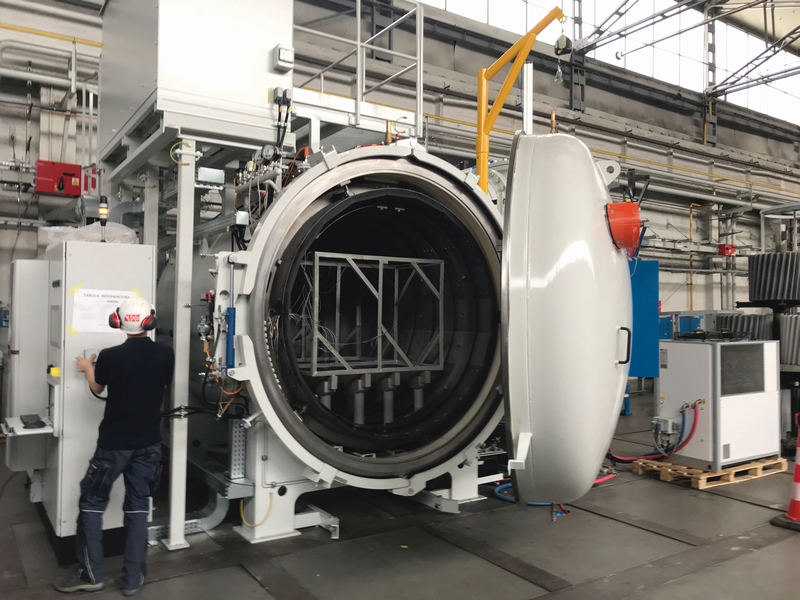
Our capabilities
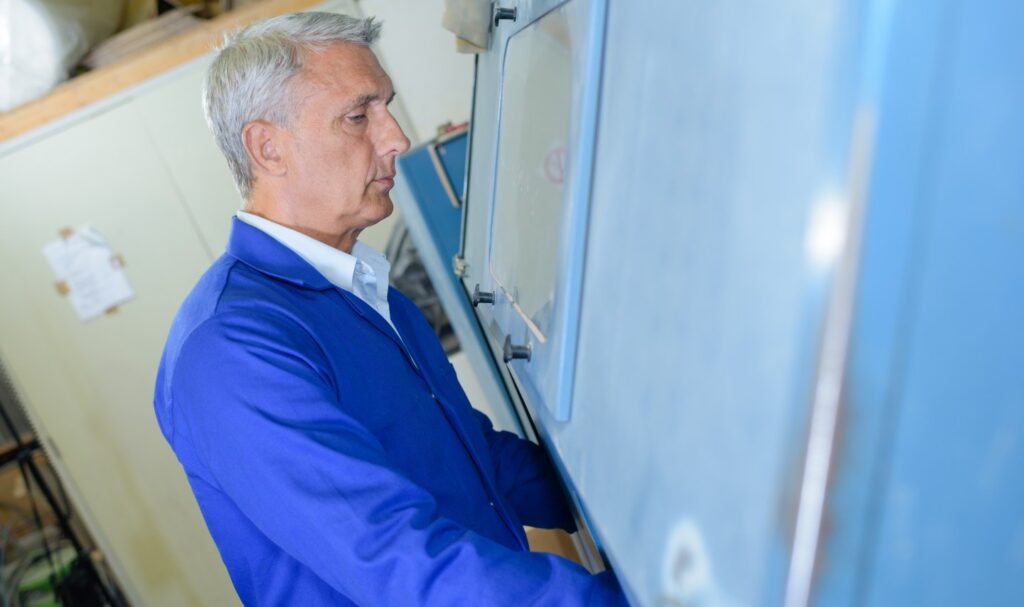
Blasting
In our blasting booths, we have the capability to clean various surfaces and remove strong contamination such as coke or oil deposits. We have a wide selection of medium available, both in terms of type and mesh size.
In addition to cleaning, our spraying technologies are also used for preparation for painting. We have the most used media (ALUMINA60, 80 220, CORUND 50, 160, 180, 300, 500) and procedures according to SPM 70-51-11/12/13.
Fabricated
Machine Parts
Low and medium volume machining products: machining products with high labor requirements
Machining with different raw materials: carbon steel, stainless steel, alloy steel, non-ferrous metals, super alloys, Hastelloy-X, nimonic, tungsten, molybdenum
Perform complex manufacturing tasks: machining, assembly, special heat treatment, coating
Design and construction of unique parts, devices, machines: indexing cam, heating basket
Our capabilities
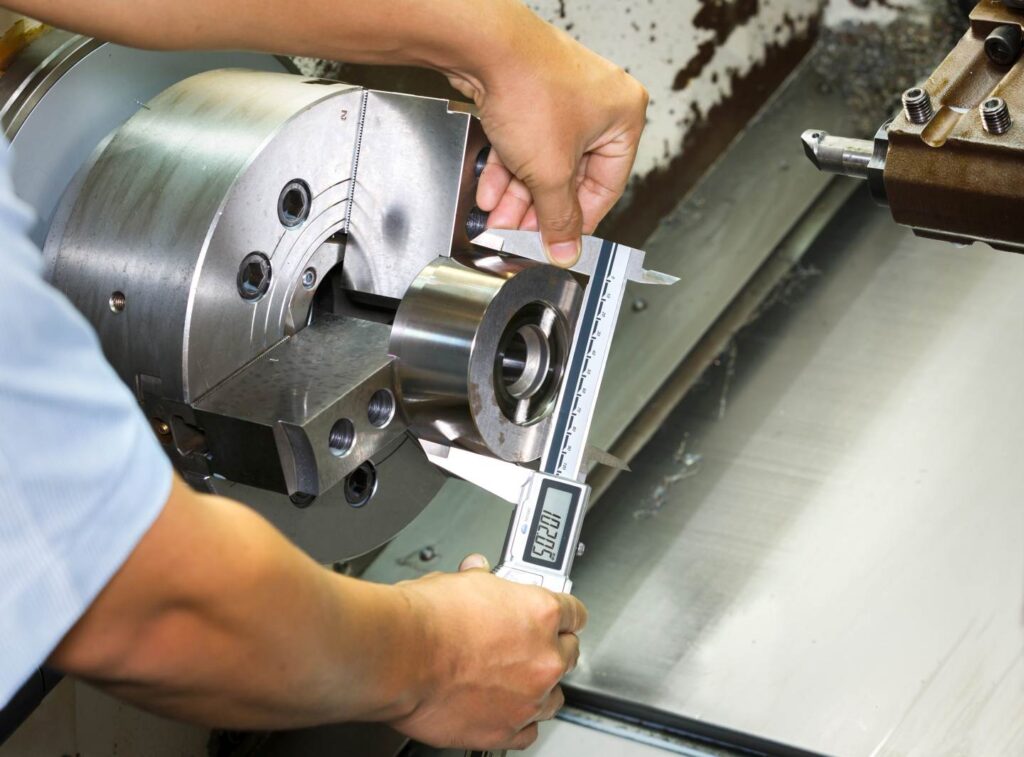
Our capabilities
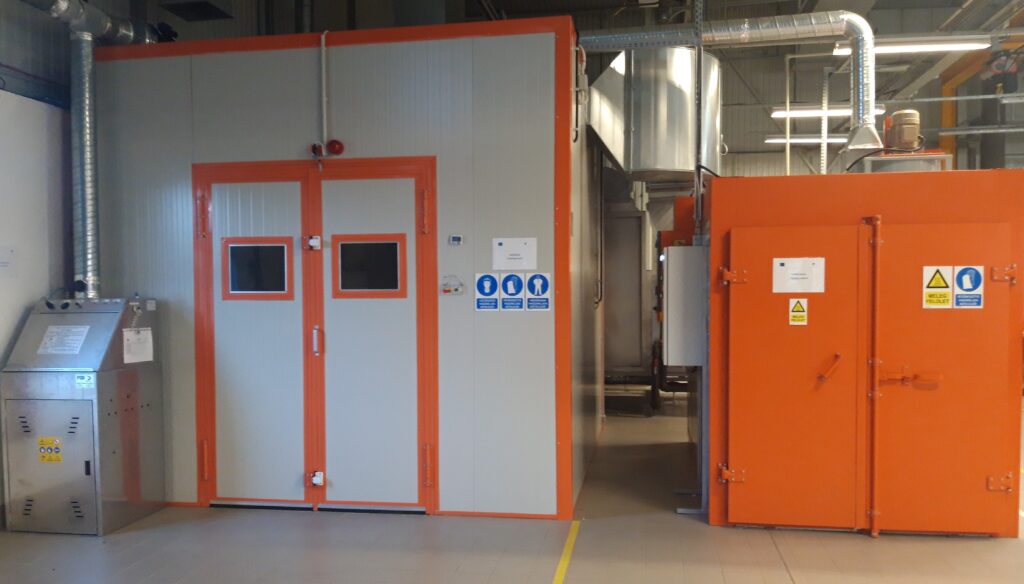
Painting Booth
Our company is equipped with superior construction of a high-strength precision paint coating system with a pumped water curtain and advanced air washing/paint collection efficiency. Equipped with a separated filter surface and side suction to achieve the perfect coating. The application of a paint coating to various parts exposed to high stress during operation. Useful internal dimensions: 3420x3420x2800 mm
Cleaning
To make the inspection of engine components effective, a proper cleaning process is essential. Aero Space Power has several chemical cleaning lines to ensure adequate cleanliness prior to inspection. A three-to-four-step process using a light alkaline cleaning in conjunction with a rinse ensures there are no contaminants and deposits that could hinder the proper inspection.
The cleaning lines meet the requirements of OEM and SAE standards. We can control the temperature, exposure time, and concentration of the solutions. We are also able to carry out in-process cleaning with the appropriate water cleaning equipment and steam cleaning based on the required SPM chapters 70-21.
Our capabilities
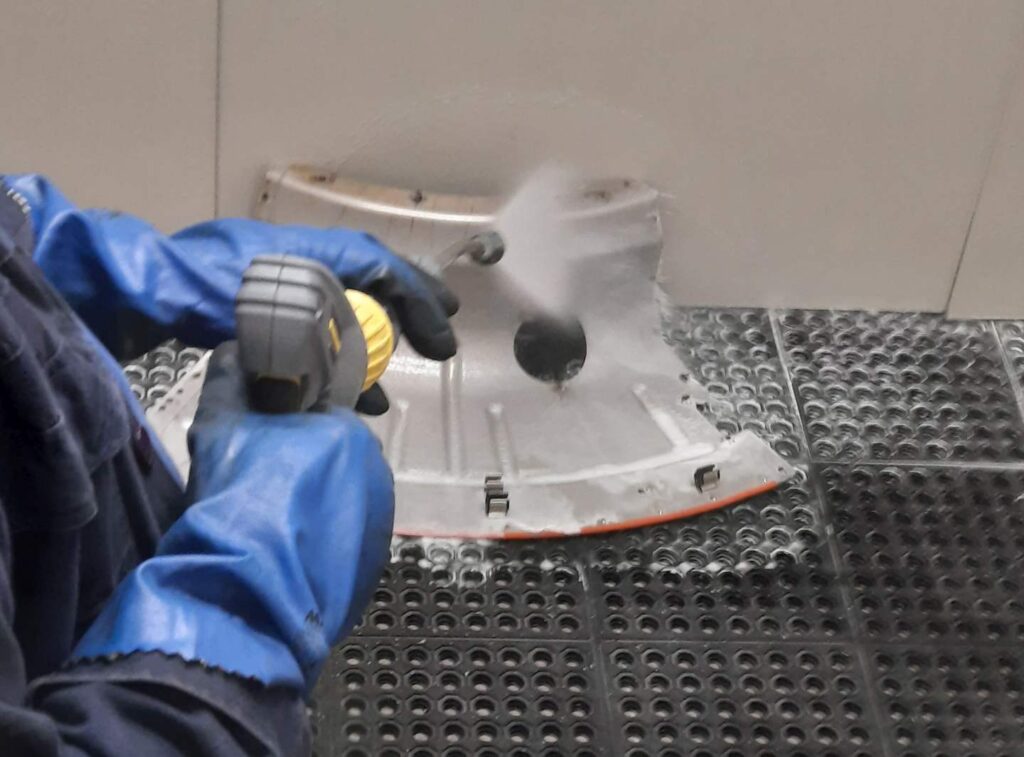