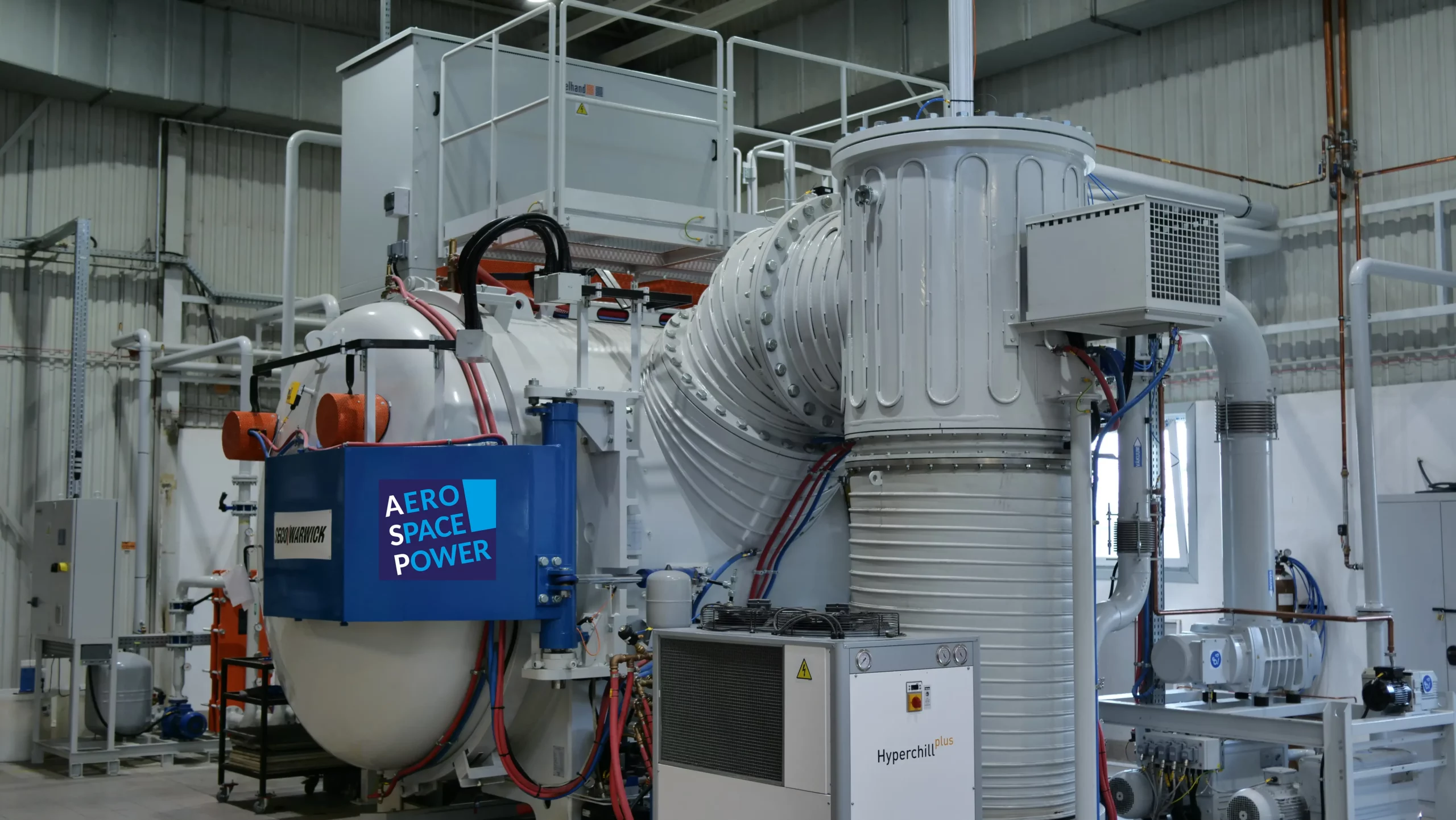
Vacuum Heat Treatment
This technology allows metal components to be heated in an oxygen-free environment, enhancing their mechanical properties and surface quality.
At Aero Space Power, we utilize this technology across multiple areas, including heat treatment of aircraft engine and gas turbine components as part of the repair process, as well as for various metal parts in other industries.
With a work chamber of 1300 x 1500 x 1000 mm, our furnace is capable of processing large-sized components, meeting the strictest industry standards.
The SECO/WARWICK VECTOR® vacuum heat treatment furnace is a single-chamber, horizontally oriented, gas-cooled system.
The Furnace
Aero Space Power is committed to utilizing cutting-edge technologies in the aerospace and energy industries. We take pride in our long-term partnerships with GE Vernova and GE Aviation. As part of this collaboration, we employ the SECO/WARWICK VECTOR® vacuum heat treatment furnace, one of the most advanced and reliable systems in the heat treatment industry.
This technology minimizes surface oxidation, ensures excellent dimensional accuracy, and provides high repeatability, making it suitable for various heat treatment processes, including:
- Solution heat treatment
- AGE heat treatment
- Tempering
- Vacuum brazing
- Cleaning heat treatment
- Hardening
- Stress relieving
- Partial pressure heat treatment with argon, hydrogen, and nitrogen
Our capabilities
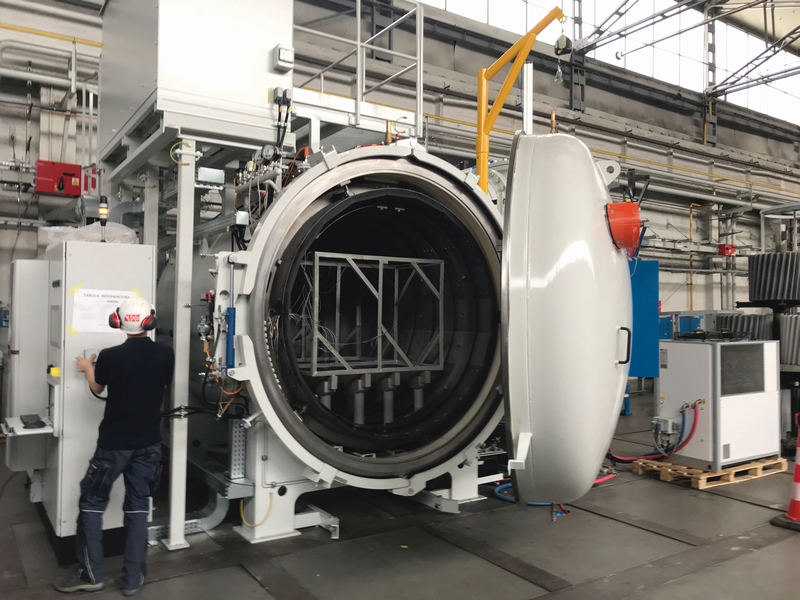
Technical Specifications & Advantages
- Class 2 certification according to AMS2750 standards.
- Work chamber size: With dimensions of 1300 x 1500 x 1000 mm, the furnace is capable of processing large components, making it ideal for industries working with oversized parts.
- Maximum load capacity: The furnace can handle up to 2000 kg, allowing for the simultaneous treatment of large or heavy components, increasing productivity and reducing cycle times.
- Maximum temperature & uniformity: A maximum operating temperature of 1300°C and a ±5°C uniformity ensure precise and consistent heat treatment, essential for high-quality final products.
- Operating vacuum: The furnace operates at 1 x 10⁻⁴ mbar, enabling high-purity processes that minimize oxidation and unwanted reactions, ensuring clean and smooth component surfaces.
- Cooling gases & pressure: The system uses nitrogen and argon as cooling gases and supports a maximum cooling pressure of 0.5 bar absolute, providing a flexible and efficient cooling process adaptable to various materials and geometries.
- Protective gases during heat treatment: Capable of heat treatment in argon, nitrogen, and hydrogen atmospheres at a maximum pressure of 0.3 bar.
- Cooling capabilities: Supports both rapid gas cooling and controlled gas cooling.
Applications
The VECTOR® vacuum heat treatment furnace is highly versatile and can be applied across multiple industries:
- Aerospace: Heat treatment of aircraft engine components.
- Energy sector: Heat treatment of turbine and generator parts.
- Automotive industry: Enhancing hardness and durability of engine parts, transmission components, and other critical elements.
- Tool manufacturing: Improving hardness and wear resistance of tools and molds, essential for longevity and performance.
Environmental Benefits
The use of vacuum technology offers significant environmental advantages:
- Reduced emissions: By using vacuum as a protective and process atmosphere, the system eliminates harmful process gases, preventing their release into the environment.
- Energy efficiency: Enhanced thermal insulation and energy-efficient electrical components (e.g., IE3-class motors, inverter control) help reduce energy consumption.
This state-of-the-art technology ensures high-quality, sustainable, and efficient heat treatment solutions, supporting the most demanding industrial applications.