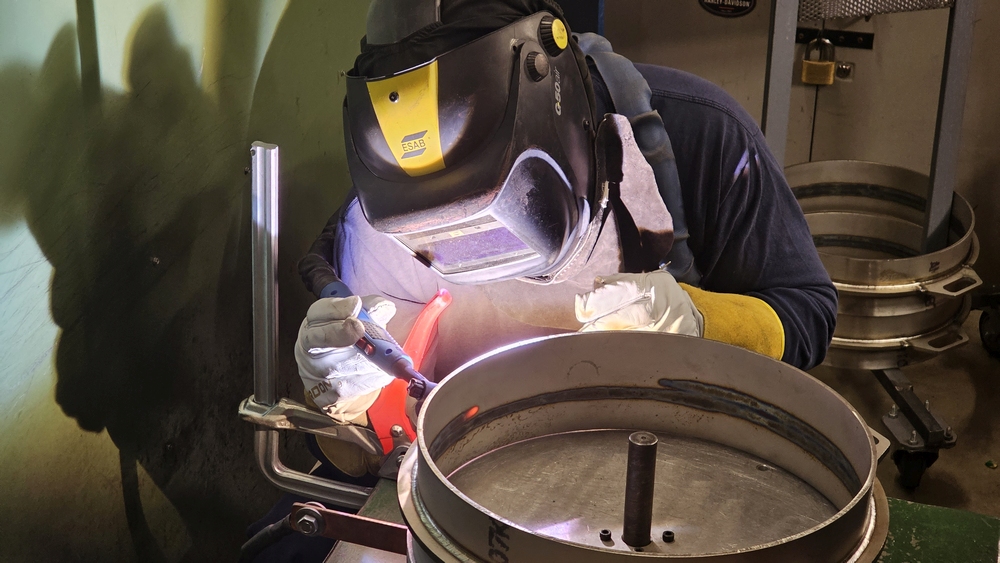
New-Make
Besides our extensive repair operation, ASP makes brand new components used in the combustion and the hot-gas-path area in Gas turbines. Our main new-make portfolio consists of Liner aft ends, liner stop rings, and transition piece extender sleeves for various turbine types. Our team’s experience allows us to ensure the quality of these high-value products. Our partner trusts us with an ever-growing demand and product scope.
We specialize in welding, heat treatment, and machining of superalloys, including Inconel, Hast-X, and special stainless steel used in these applications.
New gas turbine components: Liner AFT, TP Sleeve, and Liner Stop Ring
OUR CAPABILITIES
Liner AFT END
TP Sleeve
Liner stop ring
Our capabilities
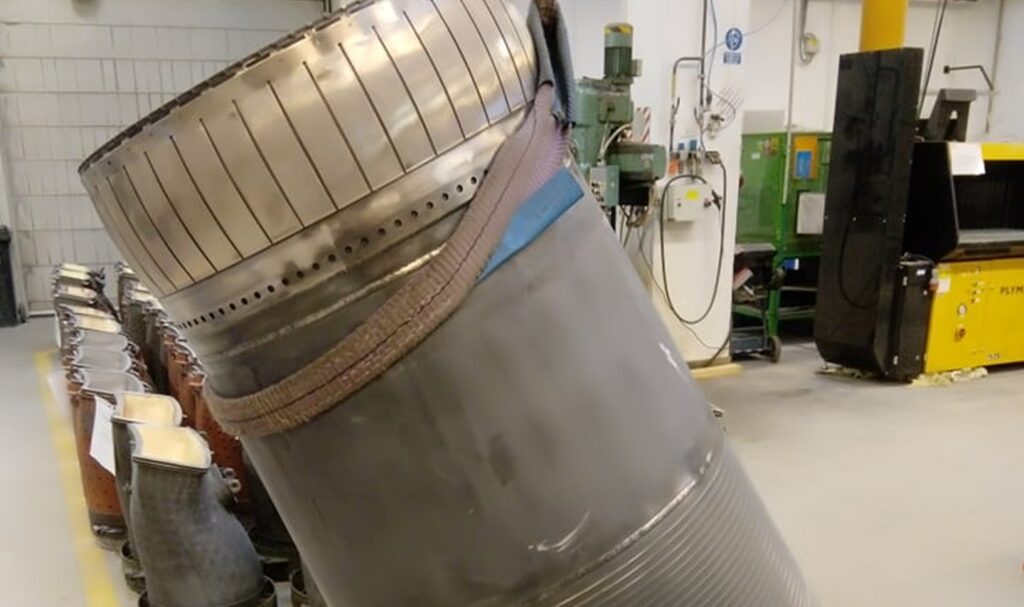
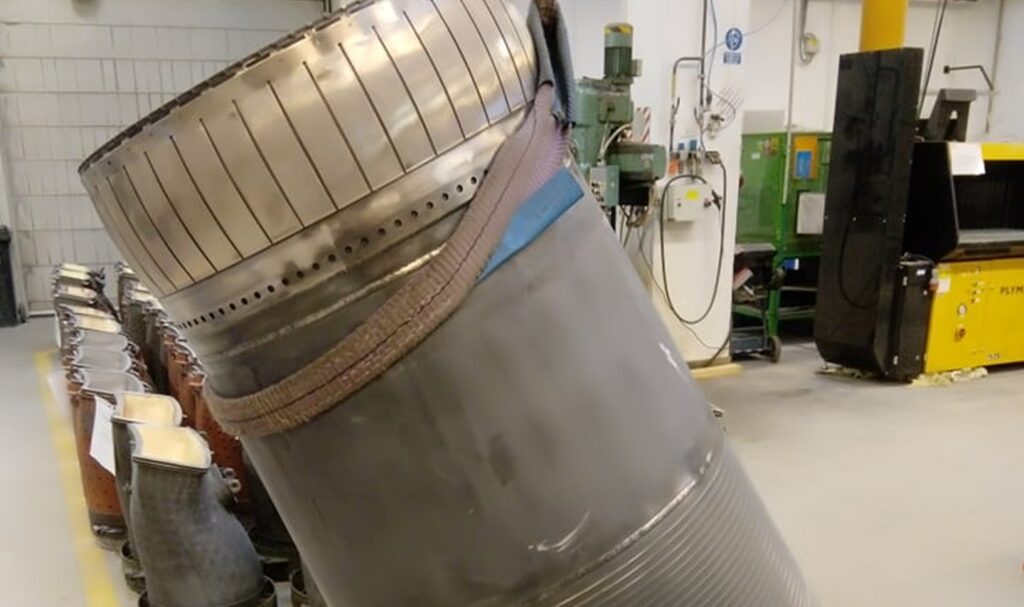
Liner AFT END
The combustion process occurs within the combustion liners, which play a critical role in supplying heat through the controlled combustion of large amounts of fuel and compressed air. This process converts chemical energy into mechanical energy in a gas turbine. Due to the extreme heat loads, a Thermal Barrier Coating (TBC) is applied inside the shell to protect components from thermal degradation.
As a non-standard test method, Eddy current testing is used to detect discontinuities at specific interfaces, ensuring structural integrity.
Repair documentation must be well-structured, with high-resolution photos attached to provide a clear record of findings and corrective actions.
During workshop visits, components must be thoroughly cleaned—typically through grinding or grit blasting—before inspection, allowing for an accurate assessment of repair needs. The maintenance and repairability evaluation includes disassembly, penetrant testing with red dye, and both dimensional and visual inspections.
TP Sleeve
The TP Sleeve is a critical component of the Transition Piece (TP), located at its forward end. Its primary function is to position and securely attach the TP to the engine body, ensuring stability and proper alignment during operation.
Manufactured from raw materials, the TP Sleeve undergoes a precision-driven process requiring advanced machinery and equipment. Throughout production, the part must meet strict quality standards, carefully monitored by Tungsram’s highly skilled operators.
The manufacturing process begins with rolling the raw sheet metal to form the required ring shape. Next, the component undergoes TIG welding, calibration, and expansion to achieve its final dimensions. To ensure defect-free quality, the part is subjected to a thorough inspection by Fluorescent Penetrant Inspectors, identifying any surface irregularities before final approval.
Our capabilities
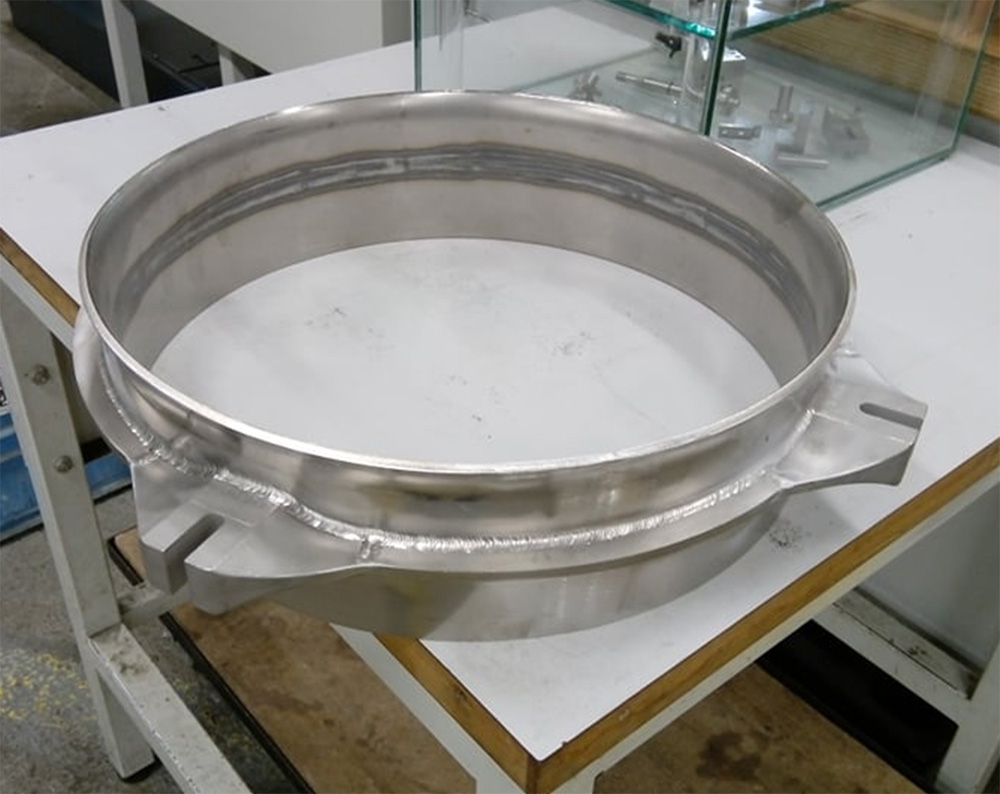
Our capabilities
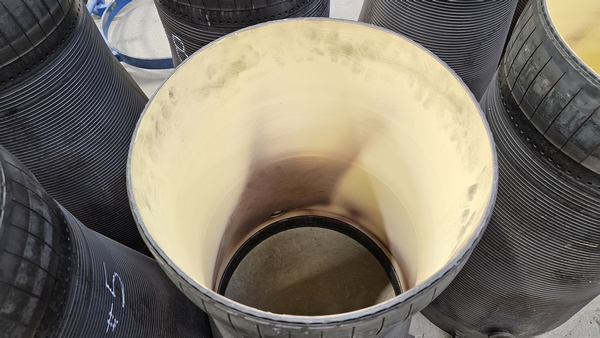
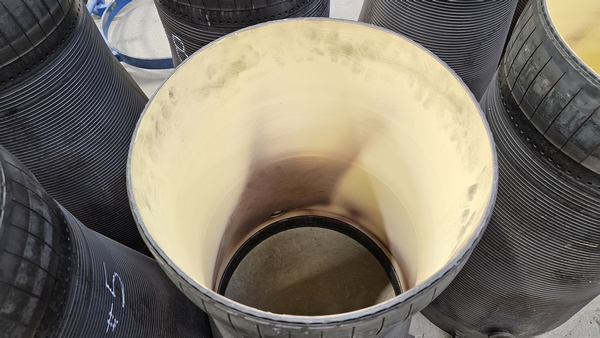
Liner stop ring
The liner stop ring is a critical component in aviation gas turbines, ensuring proper alignment and positioning of the combustion liner within the engine casing. Over time, it is subjected to high temperatures, mechanical stress, and oxidation, leading to wear, deformation, or cracking. Proper inspection and repair are essential to maintain engine performance and safety.
The repair process begins with thorough cleaning, typically using grit blasting or chemical cleaning to remove carbon deposits and oxidation. A visual and dimensional inspection follows, often supplemented by fluorescent penetrant inspection (FPI) or eddy current testing to detect cracks or discontinuities.
If damage is identified, the liner stop ring may require welding, machining, or material buildup to restore its original shape and structural integrity. After repairs, the component undergoes heat treatment, stress relief, and final quality inspections before being reinstalled. Proper documentation and high-resolution images ensure compliance with aviation safety standards.