
Repair
Our company is committed to the highest standards of quality and precision, whether it involves refurbishing existing parts or manufacturing specific components. Our services include the maintenance and production of various components that meet the strictest industry standards. Our experienced engineers and technicians apply advanced technologies to provide the best solution for our customers, thereby contributing to the long-term, uninterrupted operation of gas turbines and the energy industry. We take particular pride in our long-term partnership with the industry leader, GE Vernova, in this category.
The repair and manufacturing of gas turbine components play a crucial role in energy production, ensuring the reliability and efficiency of engines.
Our capabilities
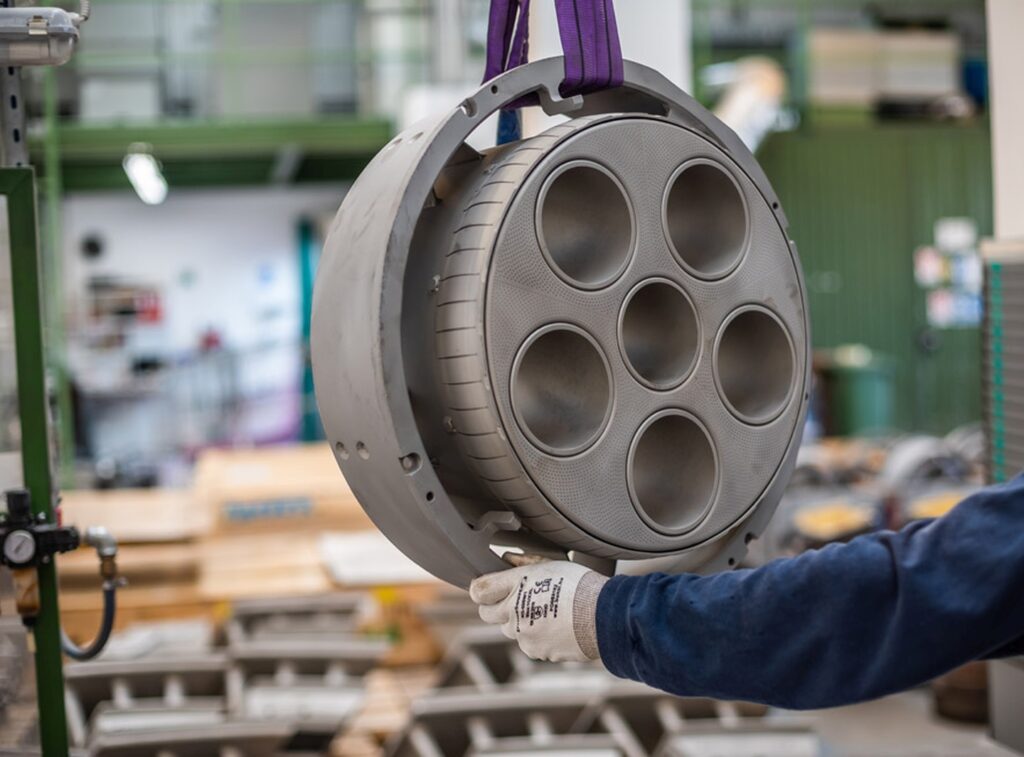
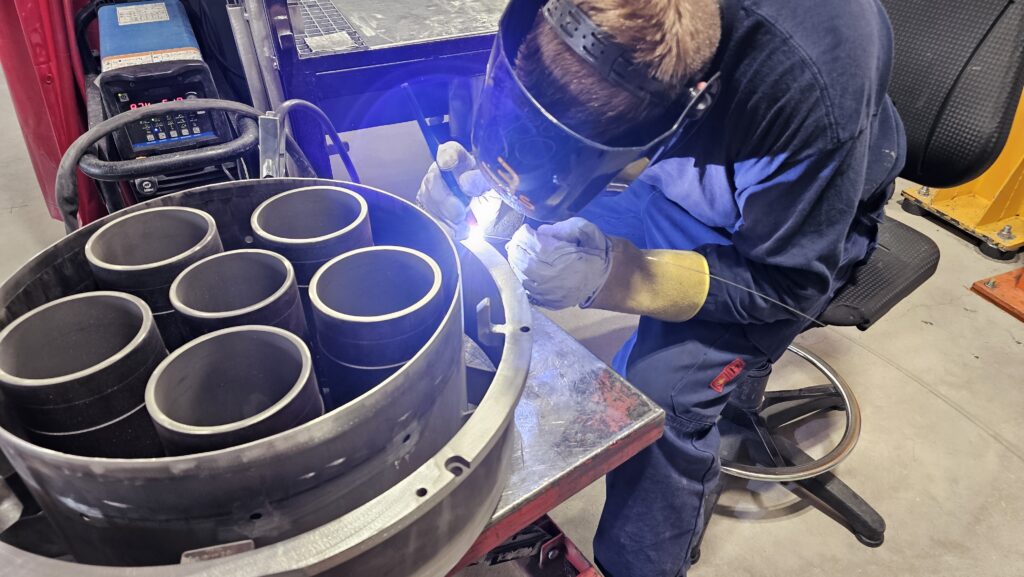
Cap
Combustion Chamber Cap (Cap) Repair Capabilities
During our maintenance operations, we perform the following steps:
- Cleaning: Sandblasting or grinding to remove combustion deposits, followed by visual inspection for defect detection.
- Non-Destructive Testing (NDT): Penetrant testing (PT) to detect cracks. Eddy current testing (ET) to uncover material structural defects.
- Welding Repairs: Precision welding using TIG (GTAW) or plasma transfer arc welding (PTA) to repair cracks.
- Heat Treatment: Restoring structural integrity.
- Final Inspection: Geometric measurements, visual inspection, and execution of necessary quality control processes.
We aim to perform combustion chamber cap repairs with the utmost care and precision. Our workshop is equipped with advanced machinery, and we have experienced specialists who understand the typical stresses and failures that these components are subjected to.
READ MORE
Combustion Chamber Cap (Cap) Role and Material Use in Gas Turbines
The combustion chamber cap (Cap) is one of the most critical components of the gas turbine’s combustion section. Its role is to stabilize the combustion process of the fuel-air mixture and control the internal pressure and temperature of the combustion chamber. This component is directly connected to the fuel nozzles and the combustion liner tubes, while also serving a thermal protection and structural role.
The combustion chamber cap is typically made from nickel-based superalloys (such as Inconel 718 and Hastelloy X), which offer excellent resistance to high temperatures and oxidation corrosion. The cap is coated with a thermal barrier coating (TBC), which may be a ceramic-based YSZ (yttrium-stabilized zirconium dioxide) coating. The cooling holes and internal channels ensure even heat distribution and protection against overheating.
Typical Failure Modes
During operation, several types of failures may occur in the combustion chamber cap, mainly due to extreme temperature and pressure fluctuations:
- Thermal Fatigue: Cracks can develop due to continuous thermal cycles, particularly around the cooling holes.
- Oxidation and Corrosion: At high temperatures, an oxide layer forms on the metal surfaces, gradually weakening the material structure.
Power Nozzle
Power Nozzle Repair Capabilities
Based on the extent and quality of the damage, our experts define the work area as medium or heavy during the inspection process.
- Surface Cleaning: Sandblasting or chemical cleaning to remove oxidation and contaminants.
- Non-Destructive Testing (NDT): Ultrasonic (UT) and eddy current (ET) testing to detect cracks.
- Welding Repairs: Precision TIG welding technology used to restore cracks. The number of welded areas determines whether the work is classified as medium or heavy.
- Heat Treatment: Stress-relieving heat treatment to reduce material stresses.
- Final Inspection: Geometric measurements, visual inspection, and necessary quality control processes are carried out.
Since cracks often develop around the gas outlet holes on the edges of the nozzle blades, the repair of these components is carried out with great care and attention to ensure that the nozzle functions perfectly after the repair process.
Read more
Power Nozzle Role and Material
Use in Gas Turbines The power nozzle is one of the most critical components of the gas turbine, responsible for directing and accelerating the flow of hot combustion gases. Power nozzles control the flow speed and the direction of the gas, thereby maximizing the turbine’s efficiency. The design of the component directly impacts the performance and fuel efficiency of the gas turbine.
Nickel-based superalloys, such as Inconel 738 or René 80, are typically used in the manufacturing of power nozzles, as they offer excellent heat resistance and mechanical strength. The purpose of selecting these materials is to ensure they can withstand high thermal loads, oxidation, and corrosion. The component is equipped with internal cooling channels that promote even cooling and reduce thermal stresses.
The operating environment of the power nozzle presents extreme challenges. Continuous temperature cycles can cause thermal fatigue, leading to the formation of fine cracks in the material’s microstructure. High-speed combustion gas flow can cause erosion, especially on the edges and around the cooling holes’ edges, resulting in gradual material loss. Additionally, oxidation and corrosion processes can weaken the material’s integrity over the long term, particularly at high temperatures.
Typical Failure Modes
- Thermal Fatigue: Temperature fluctuations can cause cracks, especially in the root zones.
- Oxidation and Corrosion: Over time, an oxidation layer can form, reducing the material’s strength.
- Erosion: Material loss caused by high-speed gas flow.
- Crazing: Microstructural fractures, especially at welded joints.
Our capabilities
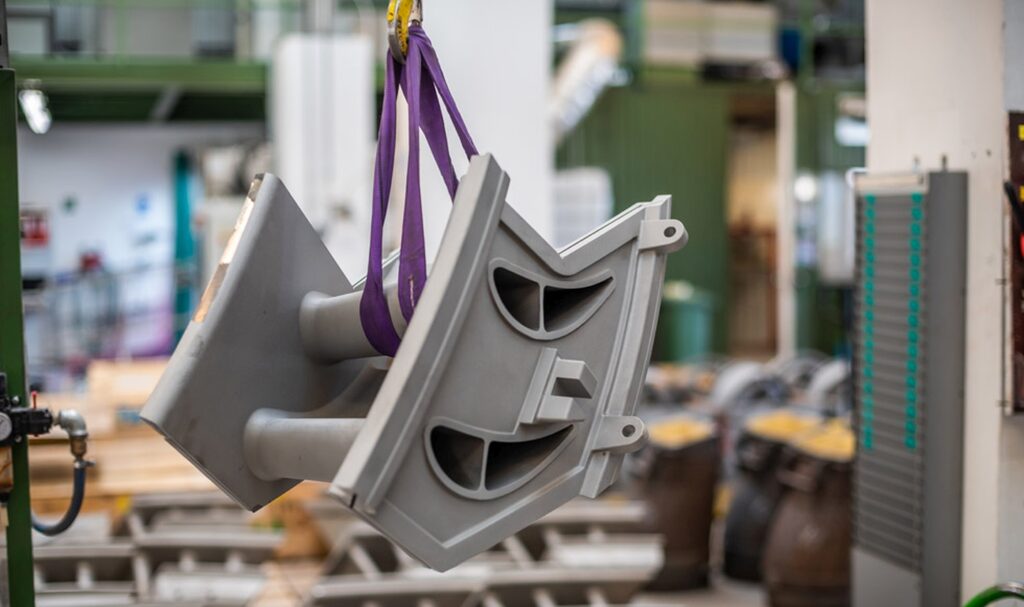
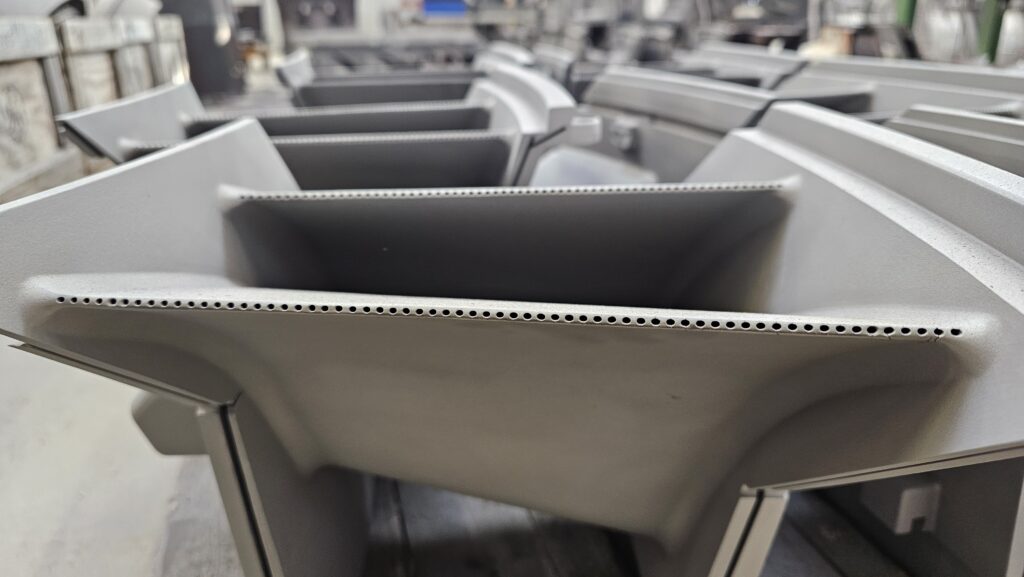
Our capabilities
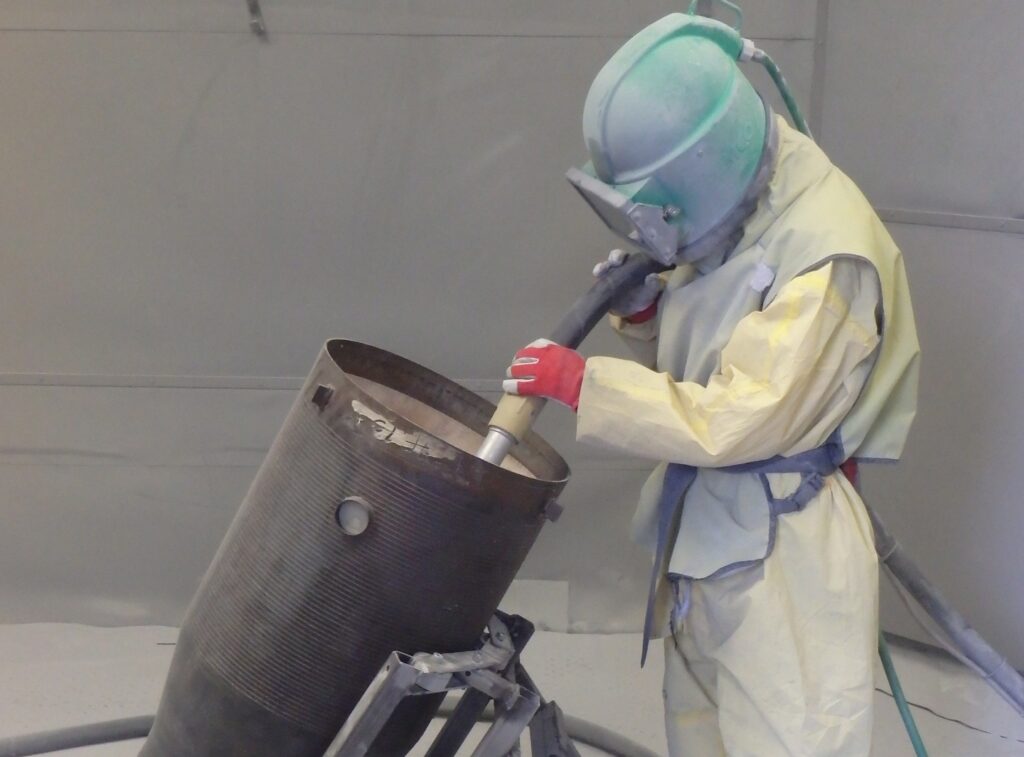
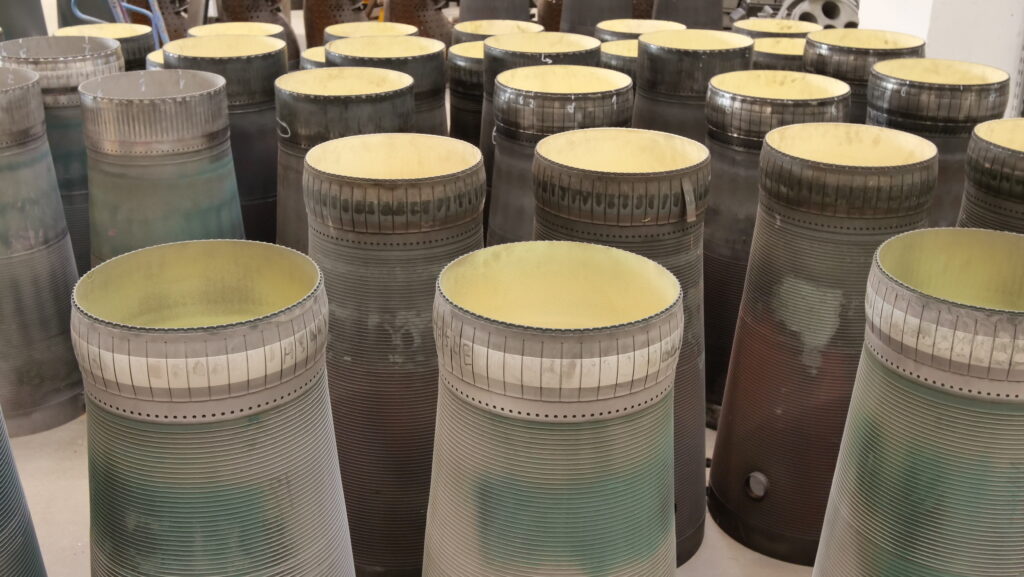
Liner
Flame Tube (Liner) Repair Capabilities
- Disassembly: As part of the maintenance/repairability inspection, the units are disassembled.
- Surface Cleaning: The special thermal protective coating on the interior surface of the liner is removed using sandblasting and grinding techniques, with particular attention paid to ensuring the underlying pipe wall is not damaged during the process.
- Non-Destructive Testing (NDT): Penetrant testing and visual inspection to detect cracks.
- Welding: Precision TIG (GTAW) welding technology is applied to repair cracks.
- Heat Treatment: Stress-relieving heat treatment to reduce material stresses and restore structural integrity.
- Final Inspection: Geometric measurements, visual inspection, and the necessary quality control processes are carried out.
Our experienced specialists use precision welding techniques during the repair process. We follow strict quality control protocols to ensure the reliability and long-term operational performance of the components for our partners.
READ MORE
Flame Tube (Liner) Role and Material Use in Gas Turbines
The flame tube (liner) is one of the key components of the gas turbine combustion chamber, serving as the primary location for the combustion process, where extreme temperature conditions, exceeding 1500°C, prevail. Its role is to provide an optimal environment for the combustion of the fuel-air mixture and to direct the flow of combustion gases towards the turbine. The design of the flame tube plays a critical role in heat distribution and the maintenance of temperature balance, which directly impacts the efficiency and lifespan of the turbine.
The flame tube is typically made from heat-resistant nickel-based superalloys and is coated with a thermal barrier coating (TBC). Cooling holes and perforated sections on the interior surface help achieve optimal distribution of cooling air, reducing the risk of thermal fatigue.
Typical Failure Modes
- Thermal Fatigue: Continuous thermal cycles can lead to cracks, particularly around the cooling holes.
- Oxidation and Corrosion: In a high-temperature environment, an oxidation layer forms, which can lead to material loss over time.
- Thermal Stress Cracks: Cracks in the material structure caused by rapid temperature changes.
- Erosion: Material loss due to the flow of combustion gases, which reduces the thickness of the component’s internal coating.
Floating seal
Floating Seal Repair Capabilities
- Cleaning: Removing any contaminants from the components.
- Disassembly: Separating the three welded segments using a grinding process.
- Seal Replacement: Removing the old seal and installing a new one.
- Geometry Inspection & Correction: If necessary, cold forming is used to press the components into a specialized mold to restore their original dimensions.
- Welding Repair: Using TIG welding, the three components are reassembled with the new seal, ensuring precise alignment in a reference mold.
- Final Inspection: Conducting geometric measurements, visual inspections, and all necessary quality control processes.
Role of Floating Seals in Gas Turbines
Floating seals are located at the rear end of the connecting section, where they join the turbine casing. Their primary function is to prevent the mixing of hot combustion gases and cooling air. By maintaining an effective pressure differential between different turbine sections, they contribute to the system’s optimal performance and efficiency.
These seals are typically made from heat-resistant metal alloys and are designed to withstand extreme temperature fluctuations and mechanical stress. Their floating design allows for self-adjustment, compensating for thermal expansion.
Typical Failure Modes
- Wear: Material loss due to continuous friction, reducing sealing efficiency.
- Thermal Fatigue: Cracks caused by repeated thermal cycles, particularly in thin metal sections.
- Deformation: Shape distortions from thermal loads, leading to reduced sealing capability.
- Oxidation: Formation of an oxide layer at high temperatures, gradually weakening the material structure.
Our capabilities
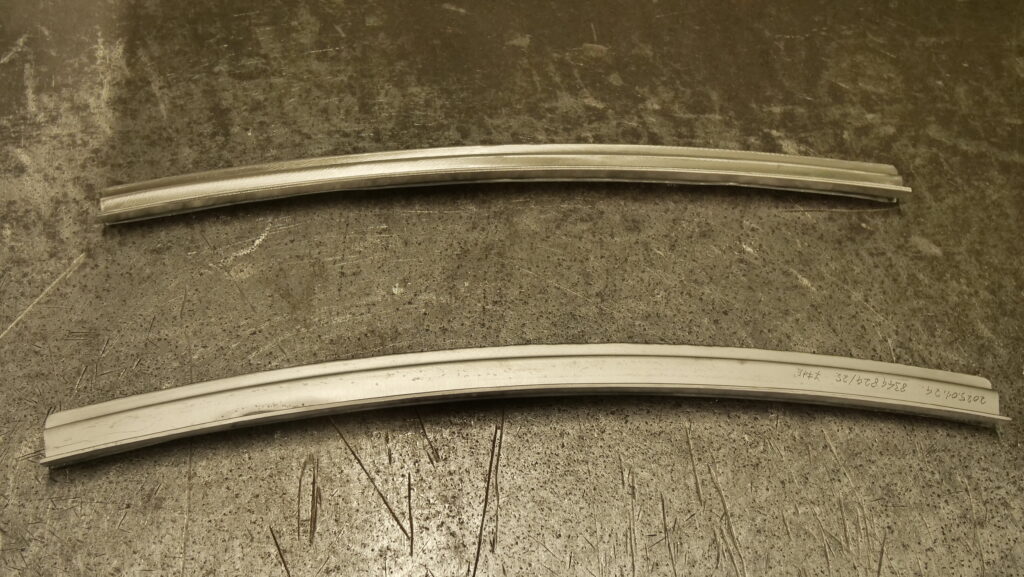
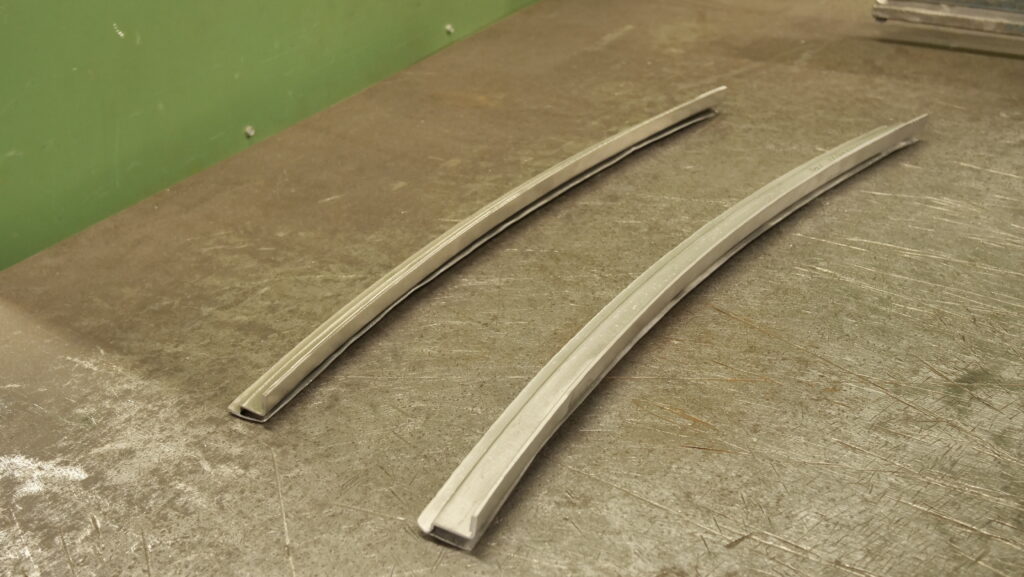
Our capabilities
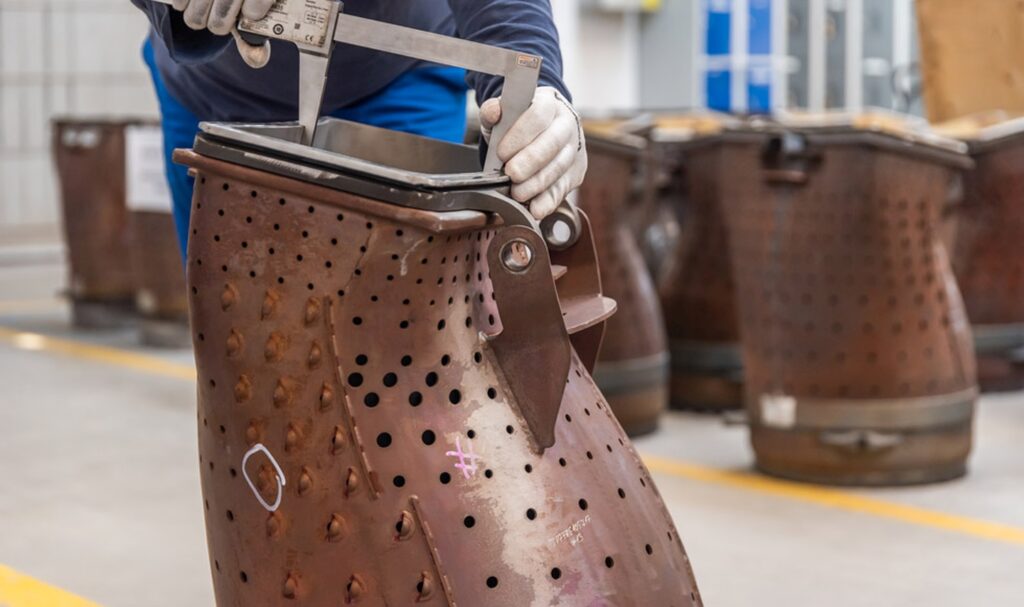
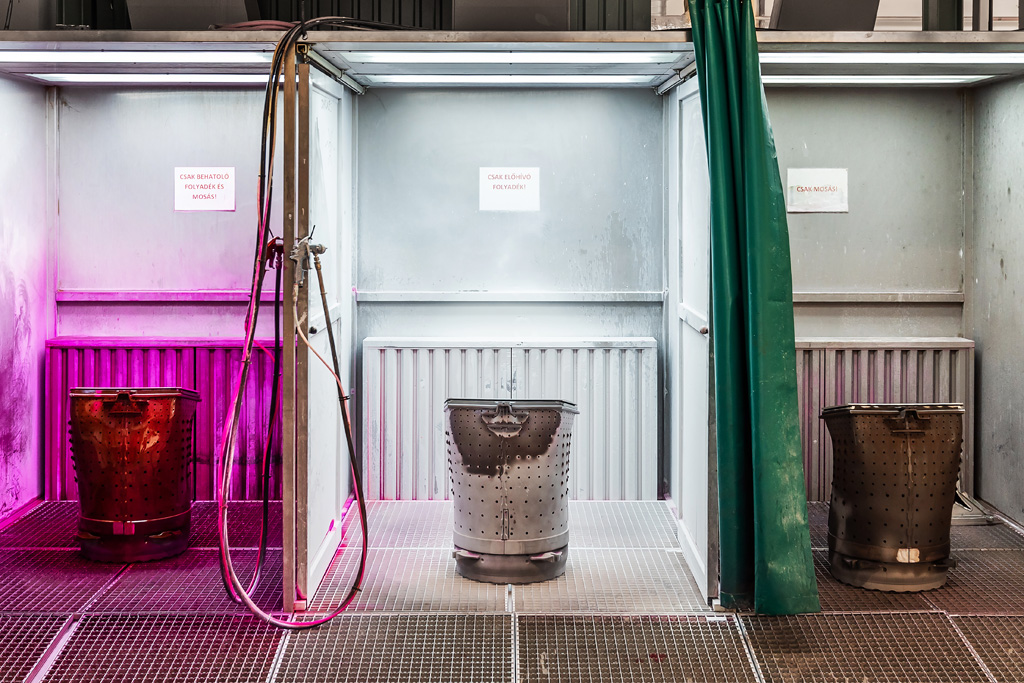
Transition piece
Maintenance and Repair Services
Our company offers comprehensive maintenance and repair services for transition pieces:
- Cleaning and Preparation: We thoroughly clean components through meticulous grinding and abrasive blasting to remove the Thermal Barrier Coating (TBC) and contaminants, preparing the surfaces for subsequent inspections.
- Inspections: We conduct visual and dye penetrant inspections to accurately identify damaged areas.
- Weld Repairs: Our experts perform necessary repairs using Tungsten Inert Gas (TIG) welding with argon shielding gas, ensuring the quality and durability of the welds.
- Geometric Verification and Measurements: Due to the significant thermal loads experienced during welding, it is essential to perform geometric verification and precise measurements of the components, which are carried out by our experienced professionals.
READ MORE
Function and Role
The primary function of the transition piece (TP) is to direct hot gases at the appropriate angle and velocity to the turbine blades, thereby optimizing the energy generation process within the turbine. This contributes to enhancing the performance and efficiency of the gas turbine.
Materials and Technical Characteristics
Transition pieces are manufactured using heat-resistant alloys capable of withstanding high-temperature and high-pressure environments. These materials are typically nickel- or cobalt-based superalloys, known for their excellent mechanical properties and corrosion resistance. TPs are coated with a Thermal Barrier Coating (TBC), which further increases their thermal resistance and lifespan.
Common Failures
During operation, transition pieces face several challenges that can lead to failures:
- Thermal Fatigue: Material fatigue caused by temperature fluctuations can lead to crack formation.
- Oxidation and Corrosion: In high-temperature environments, material oxidation and corrosion can reduce the component’s lifespan.
- Mechanical Damage: Vibrations and loads during operation can cause deformations or cracks.